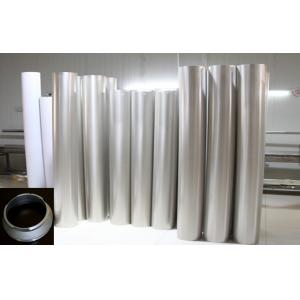
Add to Cart
Rotary Screen Clinder Textile Machinery Spare Parts High Temperature Resistance
Textile Machinery Spare Parts:
Pepeat | 640 725 918 914 1018 1206 1450 16780 | ||
Mesh | Thickness(μm) | Open Area (%) | Hole Diameter |
100 | 105-110 | 15-17 | 74 |
125 | 100-105 | 14-16 | 79 |
As previously noted, the flooding and printing action on a rotary system is all part of the same continuous motion, and separate strokes for these functions are not required. The situation is a little different with flatbed presses. On a flatbed press, printing is a two-step process that involves a pass over the screen by the floodbar to fill mesh openings with ink, followed by a squeegee pass to bring the stencil and substrate into contact for ink transfer. Not only does this approach reduce printing times, but it also removes the floodbar as a variable from the printing process.
Rotary vs. flat screen printing
Unique rotary screens
We offer a complete consumables programme, StandardScreen, Special Screens, endrings, lacquers and chemicals that comply to rigorous quality and sustainability specifications.produced its first flat-screen textile-printing machine over half a century ago. Ten years later, we unveiled our revolutionary rotary screen printing concept. This was an immediate success, and is now used for printing most of the world’s textiles.
Delivery time: within 10 to 25 days
Package:plywood cases or as you required
exhibition: